A Comprehensive Comparison of 13Cr Steel and Super 13Cr Steel: Unraveling Performance and Reliability
A Comprehensive Comparison of 13Cr Steel and Super 13Cr Steel: Unraveling Performance and Reliability
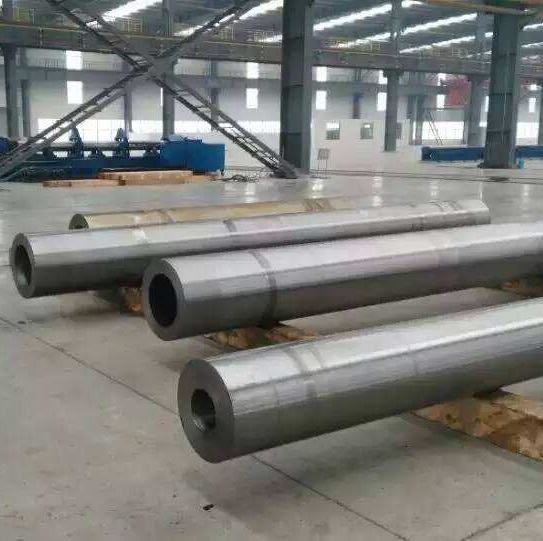
Introduction:
In the oil and gas industry, the selection of materials for downhole equipment is critical to ensure optimal performance and longevity in challenging operating conditions. Among the materials commonly used for corrosive environments, 13Cr steel and Super 13Cr steel have gained prominence for their corrosion resistance properties. This article presents a comprehensive comparison between 13Cr steel and Super 13Cr steel, analyzing various data points and performance metrics to provide insights into their respective strengths and limitations.
Chemical Composition and Mechanical Properties:
Both 13Cr steel and Super 13Cr steel are martensitic stainless steels designed for high strength and corrosion resistance. The primary difference lies in their chemical composition and alloying elements. While 13Cr steel typically contains around 12-14% chromium, Super 13Cr steel incorporates additional elements such as nickel, molybdenum, and tungsten, enhancing its corrosion resistance and mechanical properties.
Corrosion Resistance:
Corrosion resistance is a crucial factor in downhole equipment performance. Super 13Cr steel demonstrates superior resistance to corrosion, particularly in aggressive environments containing high concentrations of chlorides, carbon dioxide, and hydrogen sulfide. This advantage stems from its higher chromium content and the presence of additional alloying elements, which form a more protective passive oxide layer on the steel’s surface.
Mechanical Strength and Toughness:
When it comes to mechanical properties, both 13Cr steel and Super 13Cr steel exhibit high strength and toughness. However, Super 13Cr steel often surpasses 13Cr steel in terms of tensile strength, hardness, and impact resistance due to its enhanced alloying elements. This superior mechanical performance allows Super 13Cr steel to withstand higher loads and stresses in downhole environments.
Wear and Erosion Resistance:
In applications where wear and erosion are significant concerns, Super 13Cr steel has demonstrated enhanced resistance compared to conventional 13Cr steel. The presence of alloying elements like tungsten and molybdenum improves the steel’s resistance to abrasive particles, enhancing its durability and reducing the risk of surface degradation.
Sour Service Performance:
In sour service environments containing hydrogen sulfide, Super 13Cr steel has proven to be more resistant to sulfide stress cracking (SSC) compared to 13Cr steel. The higher nickel content in Super 13Cr steel provides improved resistance against this form of corrosion, offering enhanced reliability in sour well conditions.
Application Considerations:
When selecting between 13Cr steel and Super 13Cr steel, several factors must be considered. These include the specific downhole environment, well conditions, corrosive elements present, and the expected service life of the equipment. Additionally, cost considerations and availability may also influence the material choice.
Case Studies and Data Analysis:
To further illustrate the performance differences between 13Cr steel and Super 13Cr steel, a series of case studies and data analysis can provide valuable insights. These studies can focus on parameters such as corrosion rate, mechanical properties, failure analysis, and field performance in actual downhole applications. Analyzing real-world data can help validate the advantages of Super 13Cr steel and its potential cost-saving benefits in terms of reduced maintenance and extended equipment lifespan.
Conclusion:
In the realm of downhole equipment materials, the selection between 13Cr steel and Super 13Cr steel involves a careful assessment of their chemical composition, mechanical properties, corrosion resistance, and performance in specific downhole environments. While 13Cr steel offers excellent corrosion resistance and mechanical strength, Super 13Cr steel surpasses it in terms of enhanced corrosion resistance, improved mechanical properties, wear resistance, and performance in sour service conditions. By considering the specific well conditions
, operators can make informed decisions regarding the use of either 13Cr steel or Super 13Cr steel, ensuring optimal performance, reliability, and cost-effectiveness in their oil and gas operations.